Connection Validation™ (CV) Technology’s Next Generation Aids in Producing Perfect Solder Joints for Maximum Process Control
TestEquity is an approved distributor for Metcal.
Content Source: Metcal
New and upgraded CV modes, cartridge optimization capabilities, greater traceability, increased solder joint reliability, and more are included in Metcal’s most recent CV firmware update. The update significantly enhances Connection Validation™ technology’s already unique capability. This innovation, expected to be a considerable improvement in hand soldering, is the result of years of research and input from engineers, operators, customers, and industry leaders.
Visual Solder Joint Inspection: An Outdated Method
At the workbench is where you have the highest chance of finding a bad solder joint. But for many years, either at the workstation or after the soldering process was finished, visual examination was the sole way to confirm the quality of a solder joint.
Operators at the workbench would simply inspect each joint to determine whether it appeared to be well-made and base their judgment on the fillet height and quantity, and the finish of the solder.
Yes, there are methods to inspect joints by looking at a cross-section of the soldered board or x-raying the assembly well after the assembly has really been soldered, but by then it is too late.
It was impossible to accurately validate the integrity of solder junctions at the workbench, where it was most important. Until Connection Validation™.
Connection Validation™ Outperforms Basic Visual Inspection by a Wide Margin
Operators receive instant feedback from Connection Validation™ (CV) soldering systems from Metcal when a high-quality solder joint has been created: this cutting-edge technology checks the consistency of each joint in real time and notifies the operators when the process is finished.
The need to rely on visual inspection or the operators’ intuition alone has passed.
Calculate the Intermetallic Compound (IMC) Formation of Each Joint Using Connection Validation™ Technology
Understanding intermetallic compound production is necessary to comprehend how Connection Validation™ functions.
IMC Formation Is Needed for a Reliable Solder Joint
Simply put, soldering is the process of joining two metals together with a filler material, in this case, solder. Due to the IMC’s creation, where the solder and other metals bind, the two metals are united.
To successfully attach the solder to the component termination or board substrate, proper IMC formation is necessary. The joint will be too brittle and will likely fail if the IMC is too thin. If the IMC is too thick, it will become too brittle and crack, leading to faulty joints.
The operator must strike a balance between time on the junction and tip temperature to produce a solder joint with proper IMC formation.
The IMC Formation is Calculated using Metcal CV Soldering Systems.
The Connection Validation™ system was created by Metcal to provide station operators with quick, closed-loop data on the IMC formation of each joint.
Each joint’s IMC formation is calculated as it is being produced by the CV technology, which then sends a signal to the operator via a green LED ring light built into the handpiece. The LED glows red if the junction fails the validation process or if the soldering tip dwell time extends beyond the IPC standard.
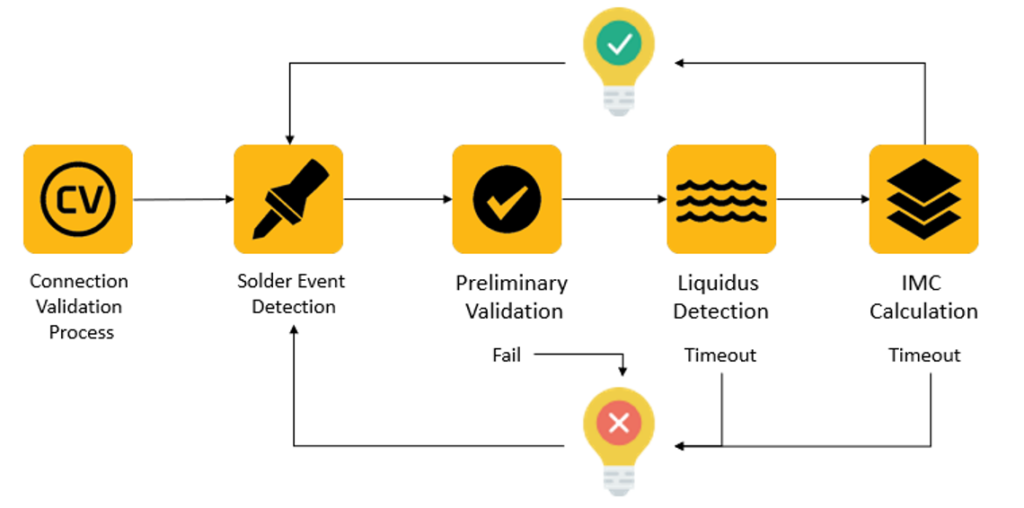
Solder Event Detection, Preliminary Validation, Liquidus Detection, and IMC Calculation are all parts of the Connection Validation™ process. The joint computations must succeed at each stage in order to receive a green signal on the handpiece.
The greatest tool for correctly assessing solder joints while they are being created is Connection Validation™.
New and improved CV modes for process control
New and enhanced functionality, including the new Connection Validation™ Modes, have been added to Connection Validation™ soldering systems with the release of the most recent software.
PRODUCTION MODE (Pcv)
In Production Mode (Pcv), the Connection Validation™ system confirms the IMC creation of each joint and alerts the operator at the conclusion of each validation cycle via the handpiece LED and an optional auditory signal:
PASS: The joint has passed validation as indicated by a green LED light and an optional audio beep.
ABORT: Red LED light and (optional) audio buzz, indicating that the event failed validation because the tip was taken off the joint too quickly.
When the tip has been on the joint for too long, a red LED light and (optionally) an audio buzz will indicate a timeout. With the use of this function, the operator can be shielded from damaging the PCB or lifting the pad. This preprogrammed time out is based on IPC Standard J-STD-001 and lasts eight (8) seconds.
Production Mode is a new enhanced mode of Connection Validation™ that relies more on the operator to complete a successful junction than earlier versions and offers faster verification. This mode is intended for seasoned users who may have found CV’s earlier iterations to be too slow. (Dual Output Mode unavailable)
TIMED MODE
A suitable time-on-joint in timed mode is set by the user or process manager dependent on the application and the temperature of the cartridge being used. The operator is informed when to remove the solder tip and move on by the CV system, which measures the dwell duration at each joint.
The Timeout Settings panel allows you to specify the time-on-joint duration, which can be between 3 and 8 seconds (IPC Standard).
When the exact dwell time and desired temperature can be predetermined, this mode is useful for ensuring operator uniformity.
CV OFF MODE
There are no active Connection Validation™ systems. Operating similarly to previous SmartHeat® systems is the CV unit.
Additional CV Improvements Boost Productivity and Process Control
The firmware upgrade adds fresh and improved functionality in addition to the new CV Modes:
Based on the specific impedance of your cartridges, the cartridge optimization system helps the CV system’s accuracy to be as high as possible.
Allowable Cartridge Settings: These settings permit or prohibit the usage of particular cartridges for better process management.
To remind users to clean their cartridge tips, there is a tip wipe reminder.
Supervisor & Operator Passcode Settings: Improved traceability and lockout
Download the CV Firmware Update Guide for additional details on all the updated and new features.
Utilize the new and upgraded CV features to their fullest
You must update your firmware to benefit from these new Connection Validation™ features.
Download the CV Firmware Update Instructions for a clear description of the firmware updating procedure. Download the CV-5200 Firmware Upgrade Loading Instructions or watch Metcal’s How-To Upgrade Your Firmware video for a thorough description of the firmware update procedure.
Contact the team at Techni-Tool to get help with the upgrade process.
