Sustainability: NOT A One-Word Solution
TestEquity is an approved distributor for PIP.
By Anthony Di Giovanni, PIP Vice President of Global Marketing
Content Source: https://us.pipglobal.com/en/about-us/news-and-events/?nID=129
Sustainable, eco-friendly, biodegradable… We can go on and on. Every day, we are bombarded with product alternatives that claim to be better for the environment – almost to the point that it’s become the norm. No doubt that these efforts are commendable, however, it’s important to acknowledge that there are no “one-word” solutions to the environmental issues we are all facing globally. History has taught us to expect that crises are often the mother of many inventions given the pivotal role technology plays. But for now, we need a more pragmatic and transparent approach.
Before the pandemic, one could argue that PPE was distantly associated with waste and pollution. However, recent images and even our own personal experiences of seeing used disposable masks and gloves discarded all over streets and job sites have tremendously elevated awareness and concern related to PPE waste.
The fact is that most PPE is derived from plastic. Even fabrics used to make protective garments are often made from synthetic polymer fibers. Fortunately, many of these fabrics are usually made with a blend of recycled fibers which is a big step in the right direction. But with eyewear, gloves and even hard hats, it’s not so easy. Eyewear and hard hats are required to sustain impacts without cracking. And since the use of recycled plastics may compromise performance, we as an industry, cannot take any chances with recycled materials.
Gloves, by far, are the most complex items when it comes to the sustainability factor. While PIP® leads the way in the use of recycled materials in glove liners, such as the G-Tek® ECOSeries™, discarding a coated seamless knit glove in a sustainable way is difficult and expensive. This is due to the fact that the palm coating and knit liner are intimately bonded together to the point where they cannot be peeled apart. This means that the coating portion would need to be cut out and separated from the knitted liner part to make the glove recyclable. PIP’s West County Gardener division recognized this difficulty many years ago, and this led them to pioneer a front-end approach with the use of P.E.T. or polyethylene-based-fibers that were derived from discarded water bottles into their gloves’ liners.
When dealing with hard hats, eyewear and face shields, they can easily be recycled by regrinding into other products, but not PPE, since PPE is required to withstand the rigors associated with life-or-death impacts. Because of this, much of the waste generated from manufacturing these items are sold as recycle-grade plastic. Even the waste from the aramid fibers that are used in the manufacturing of our cut-resistant and heat-resistant glove liners and sleeves are sold to specialists who use them as a filler when manufacturing automobile brake pads. Now, that’s ingenious!
It’s Not Always That Easy
Another main factor that impacts the recyclability potential of PPE is contamination. A significant number of gloves and garments are soiled with industrial grease or solvents that are commonly used in MRO or assembly operations. And it likely is next to impossible to determine the different types of contaminating residues or the even concentration of these contaminants. When you add in the need for decontamination to any recuperation and recycling operation, it makes the process much more expensive. That is likely why the vast majority of used gloves and garments end up in landfills.
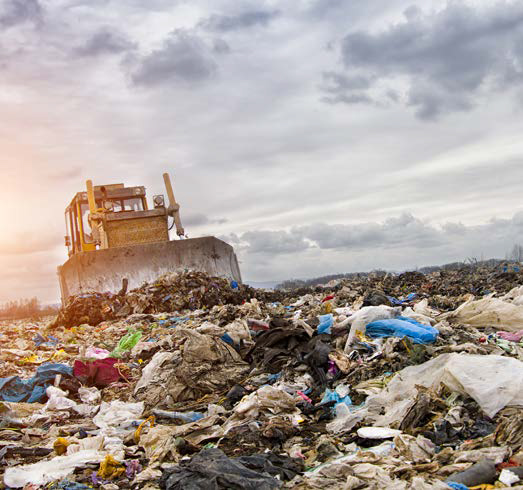
The complexity outlined here is faced by many consumable items, it’s definitely not an issue that’s unique to PPE. Today, we see many manufacturers producing items that claim to have a high degree of biodegradability, often quoting their product is 5 times or even up to 100 times more biodegradable than non-sustainable options. These claims are based on general biodegradability standards that assess the amount of biogas (a mix of methane and carbon dioxide) that’s released in lab simulated environments. This extrapolation is difficult to measure in terms of real benefits when you consider the most unknown and uncontrolled factor – the type of landfill that the PPE waste will eventually end up in. While there are more than 20 ISO and ASTM tests measuring biodegradability in various ways and environments, not much has been explored related to PPE. Making products that contain additives that speed up biodegradability is commendable. However, in our industry, these additives are typically added to nitrile which remains an inherently highly durable, oil-based synthetic polymer. More exciting technologies of a plant-based nature do exist – similar to reusable bags mandated in many European countries – and may offer a future promise. But the mechanical properties of these materials today are not anywhere near what a nitrile or PU-coated material can offer. Latex is a natural rubber that will decompose more readily than synthetics, however, concern with allergies continues to relegate this product to a less popular choice.
As a final point, which brings us back to the beginning of this blog; we need to be better educated on the terminology, as well as with the testing and decomposition technology of landfills. Whether a product is labeled “compostable,” “biodegradable,” “oxo-degradable,” or “bio-based,” it is important to know that plastics made from any of these terms may not necessarily be compostable or easily biodegradable. AND surprisingly, some plastics that do biodegrade can be made from fossil fuel-based materials.
So, What Do We Do?
PIP® believes we need to align our thinking to address PPE waste using a more “multifaceted” approach. This is why we developed the PIP® 3R™ Sustainability Program. The “Rs” stand for Reduce, Reuse, Recycle. While we are not claiming to be the originators of this concept, we would like to consider ourselves leaders in offering this as a pragmatic and transparent solution to a very big problem. Let’s start with “reusing” and “reducing,” which typically go hand-in-hand. In high-volume industrial settings. Our experience tells us that users tend to stick with one product because of lower upfront costs or, sometimes, just out of habit. PIP® has a variety of case studies demonstrating that using lower-cost gloves typically leads to exponentially more gloves being discarded because they wear faster and don’t hold up well. This also results in numerous changeouts which negatively impacts worker productivity. In some cases, when comparing low-cost generic knit gloves to coated seamless knits, workers have reported that the coated seamless knit gloves last up to 15 times longer while experiencing much better comfort and dexterity. Other comparisons involving single-use disposable gloves, which have become a staple in a majority of industries due to the pandemic, indicate that opting for a more premium extended use barrier glove, such as Grippaz®, helps reduce the total amount of gloves used by up to 5 times. Now, that’s a lot fewer gloves going to a landfill as well as a significantly smaller number of changeouts happening each day.
Reducing and reusing can also be achieved by laundering or even simple gloved-hand washing. PIP® field observations indicated that up to 40% of gloves may be prematurely disposed because they are dirty or workers just like the feeling of a “fresh pair” at the beginning of their shift. Professional industrial launderers are there to help companies initiate a glove laundering care service, but we realize that may be too much for small organizations. Nearly the same result can be achieved by providing workers with a predetermined set of gloves then asking them to wash and hang the gloves in an aerated space at the end of their shift. A habitual rotation of this process will have them working with a fresh pair for a lot longer.
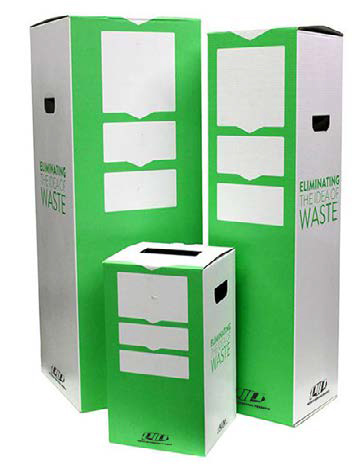
The final tenant of the PIP® 3R™ Sustainability Program is Recycle. PIP® can team customers up with onsite waste recuperators to help recycle used PPE. This concept is already very popular with batteries, light bulbs and fluorescent lights: The idea here is to divert millions of pounds of waste from landfills and incinerators each month by creating a recycling program where used PPE is collected and sent to be sorted then repurposed into new products such as rubber mats, plastic pallets and other recycled plastic products. This partnership introduces a recycling program for end-users who want to go the extra mile in ensuring that consumed PPE is disposed of in a better way. It is in the spirit of true life cycle development that PIP® seeks a more solution-oriented, front-end approach where, ideally, we know what new products will be made from spent recyclable materials.
Final Thoughts
No PPE manufacturer has an exclusive solution to waste reduction. There needs to be a multi-pronged approach that is not proprietary to anyone. It is possible that down the road, new materials can be developed that are easily recycled into tough-wearing products that stand up to the rigors and testing required for PPE or that biodegrade quickly into most landfills and may even be compostable. This is something that we all seek for the benefit of the industry as well as for the futures of our children.
